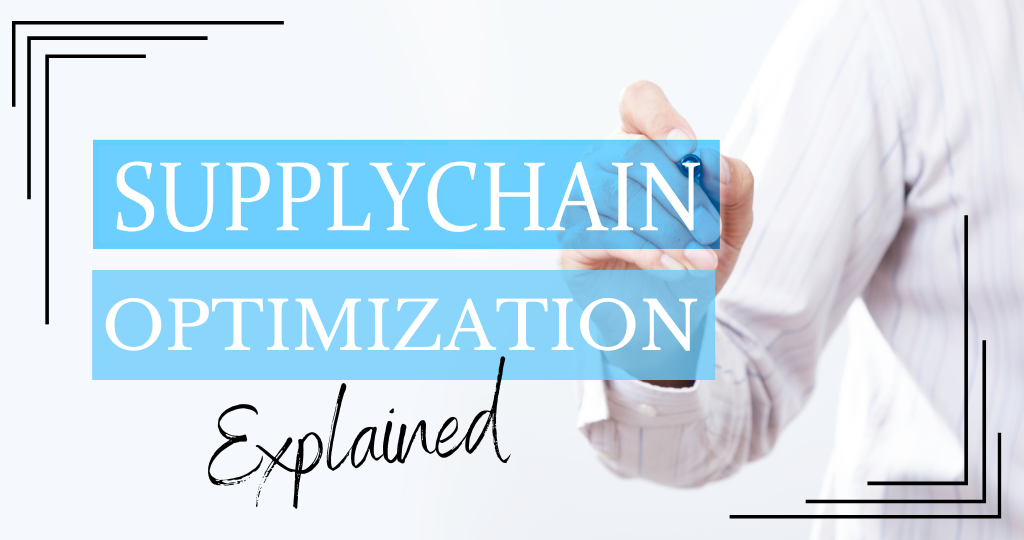
Supply Chain Optimization Explained!
Supply chain optimization is a method for bringing out the best in a specific process, function, or position without burdening the budget or hurting the supply chain’s final outcome. This method tends to identify the weak links in the overall supply chain network, give recommendations for improvements and hence, deliver quality performance.
Modern, evolved supply chains, of today, involve a tightly knit network of internal and external stakeholders. As a result, modern supply chains are sensitive to external changes, necessitating close monitoring of their costs and operational effectiveness. This is where supply chain optimization takes center stage.
How to begin with supply chain optimization?
Supply chains, of today, face a lot of challenges operating in volatile, uncertain, and complex business environments. But one constant challenge that supply chain managers have been dealing with for years, is to constantly monitor and save on logistics costs to improve overall company profitability. But supply chain optimization is beyond the scope of just money. It takes into account the factors like manpower efficiency, process effectiveness, risk factors, market situation, and of course, customer satisfaction. It’s pretty much the weighted average of the above-stated factors for the benefit of the company.
In order to make it simple for you, we have listed 5 areas that are generally in dire need of supply chain optimization solutions.
Low-performing Areas in Supply Chain
Supply chains essentially involve all the steps from moving raw materials within the premises to delivering the finished product to the customer. Though the final goal is the same, every supply chain is unique and different, in its own sense. To optimize supply chains, use this framework to identify low-performing areas and implement relevant optimization strategies.
(i) Supply Chain Inventory levels
Are you facing the problem of stockouts? overstocking? or higher inventory cost? Then take it as an alarm bell as it might be taking up a huge chunk of your logistics spending. In addition, low performance can also raise questions about the efficiency of forecasting and managing demand. So close examination of this area can ensure the right amount of inventory stock is maintained to drive high order fulfillment.
(ii) Vendor Network Analysis
Companies depend on external vendors for supply chain functions but often don’t evaluate their costs and services. If issues arise with vendors, it’s an opportunity to explore other players and conduct a comparative analysis. For example, if you have problems with logistics service providers, such as order placement, rate negotiation, or delivery status, you should consider alternative options.
(iii) Transportation segment
Transportation costs make up 40-50% of overall supply chain costs, so evaluating the processes can help save on logistics costs. The transportation of goods begins as soon as they leave the factory premises and ends as soon as they are delivered to the customer. Hence, this operation usually falls beyond the control of logistics managers. A lot of software solutions are available that can help monitor & control basic parameters like route adherence, delivery delays, driver performance, etc, to bring cost & operational efficiencies.
(iv) Monitoring on-ground operations
The basic on-ground operations such as loading, unloading, picking, and packaging are often not closely monitored with timestamps. A slight delay in any of these operations can increase the completion time for the other. For example. A slow loading/unloading process can create a bottleneck situation at the docks, increasing the waiting time of the vehicles. If this delay goes beyond a permissible level, then it can start adding up as detention costs. So, you can start by identifying the physical operations in your supply chain, examine their competence and look out for ways to bring in more efficiency.
(v) Budget setting & evaluation
Budgeting is the best way to keep a track of all supply chain spending. A clearly defined budget gives a structured framework to logistics operations. Regular audits further help the logistics budgets to stay well within the limits. The assigned budget should also be in line with the company’s goals & priorities i.e. if the company plans on reducing its carbon footprint, then higher costs should be allotted for eco-friendly packaging, green vehicles for transportation, etc.
How can supply chain optimization software help?
With advanced technologies like AI, machine learning, blockchain, and IoT, the software can integrate, simulate, and analyze the supply chain process. It can identify problem areas and offer calculated alternatives based on ROI, market structure, price, and more. This further helps the supply chains in taking informed business decisions.
This software, when implemented appropriately, brings in a lot of quantifiable & non-quantifiable benefits. The most significant of all is the end-to-end visibility of all supply chain processes, communication & financial transactions. These in turn drive the consequential benefits like improved process & manpower efficiency, supply chain sustainability adherence, optimized logistics costs, and higher profit margins.
Elixia’s Intelligent delivery orchestration platform is an advanced technology-driven, industry-agnostic solution that provides end-to-end visibility and control across all segments of logistics and supply chain. This solution optimizes supply chain processes from order booking to delivery, including invoicing, payments, driver management, and fleet handling. It provides actionable business insights that increase operational efficiency and saves logistics costs.
Want to drive supply chain optimization with Elixia?